Predictive maintenance is a transformative approach that leverages advanced technologies to predict equipment failures before they occur, allowing for timely interventions that prevent costly downtime and repairs. Among the various technologies that enable predictive maintenance, Artificial Intelligence (AI) stands out as a critical component. This article explores the role of AI in predictive maintenance, its benefits, challenges, and future prospects.
Maintenance strategies have evolved significantly over the years. From reactive maintenance, where repairs are made after a failure occurs, to preventive maintenance, which involves regular inspections and servicing, the goal has always been to minimize equipment downtime and prolong asset life. Predictive maintenance (PdM) takes this a step further by using data-driven insights to anticipate failures before they happen, optimizing maintenance schedules, and ensuring operational efficiency.
AI plays a crucial role in predictive maintenance by analyzing vast amounts of data from various sources, identifying patterns, and providing actionable insights. By leveraging AI, organizations can move from a reactive to a proactive maintenance approach, significantly enhancing productivity and reducing costs.
The Role of AI in Predictive Maintenance
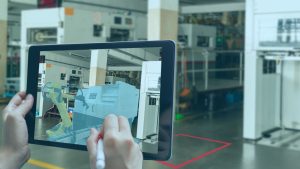
AI encompasses a range of technologies, including machine learning (ML), deep learning, and natural language processing (NLP), which can be applied to predictive maintenance in several ways:
Data Collection and Processing:
AI systems can gather and process large volumes of data from multiple sources, such as sensors, historical maintenance records, and operational logs. This data is critical for developing accurate predictive models.
Predictive Modeling:
Machine learning algorithms can analyze historical and real-time data to identify patterns and trends that indicate potential failures. These models can predict when and where a failure is likely to occur, allowing maintenance teams to take preemptive action.
Anomaly Detection:
AI can continuously monitor equipment performance and detect anomalies that deviate from normal operating conditions. Early detection of anomalies can help prevent minor issues from escalating into major failures.
Root Cause Analysis:
When a failure occurs, AI can assist in identifying the root cause by analyzing data and correlating it with known failure modes. This helps in implementing corrective measures and improving future maintenance strategies.
Optimization of Maintenance Schedules:
AI can optimize maintenance schedules by predicting the optimal time for interventions based on equipment condition and usage patterns. This reduces unnecessary maintenance activities and ensures that resources are used efficiently.
Natural Language Processing:
NLP can analyze unstructured data, such as maintenance logs and technician notes, to extract valuable insights and enhance predictive models. This helps in understanding the context and nuances of equipment behavior.
Benefits of AI in Predictive Maintenance
The integration of AI in predictive maintenance offers numerous benefits:
Reduced Downtime: By predicting failures before they occur, AI helps prevent unexpected equipment breakdowns, minimizing downtime and maintaining production continuity.
Cost Savings: Predictive maintenance reduces the need for emergency repairs and extends the lifespan of assets, leading to significant cost savings in maintenance and replacement.
Improved Safety: Timely maintenance interventions prevent catastrophic failures, enhancing the safety of operations and protecting workers from hazardous conditions.
Enhanced Efficiency: AI-driven predictive maintenance optimizes maintenance schedules, ensuring that resources are used effectively and maintenance activities are performed only when necessary.
Data-Driven Insights: AI provides valuable insights into equipment performance and health, enabling informed decision-making and continuous improvement in maintenance practices.
Challenges in Implementing AI in Predictive Maintenance
Despite its benefits, implementing AI in predictive maintenance comes with several challenges:
Data Quality and Availability: High-quality, accurate data is essential for developing reliable predictive models. In many cases, data may be incomplete, noisy, or inconsistent, affecting the accuracy of predictions.
Integration with Existing Systems: Integrating AI with existing maintenance and enterprise systems can be complex and requires seamless data exchange and interoperability.
Scalability: Scaling AI solutions across multiple assets and locations can be challenging, particularly in large organizations with diverse equipment and operational conditions.
Technical Expertise: Implementing AI requires specialized knowledge in data science, machine learning, and domain expertise in maintenance. Organizations may face challenges in acquiring and retaining such expertise.
Change Management: Transitioning to AI-driven predictive maintenance involves changes in processes, workflows, and organizational culture. Ensuring buy-in from all stakeholders and managing resistance to change is crucial for successful implementation.
AI in Predictive Maintenance
Several industries have successfully implemented AI in predictive maintenance, demonstrating its potential to revolutionize maintenance practices:
Manufacturing:
A global manufacturing company implemented AI-based predictive maintenance for its critical machinery. By analyzing sensor data and historical maintenance records, the company achieved a 20% reduction in unplanned downtime and a 15% decrease in maintenance costs.
Energy Sector:
An energy company used AI to predict failures in its wind turbines. The AI system analyzed vibration data and identified early signs of bearing failures, allowing for timely replacements and preventing costly downtime. This resulted in a 25% increase in turbine availability.
Aviation:
An airline adopted AI-driven predictive maintenance for its fleet of aircraft. By monitoring engine performance and analyzing flight data, the airline reduced unscheduled maintenance events by 30%, improving fleet reliability and reducing operational disruptions.
Future Prospects of AI in Predictive Maintenance
The future of AI in predictive maintenance is promising, with several trends and developments expected to shape its evolution:
Advancements in AI Algorithms: Ongoing advancements in machine learning and deep learning algorithms will enhance the accuracy and reliability of predictive models, enabling more precise failure predictions.
Edge Computing: The integration of edge computing with AI will allow real-time data processing and analysis at the source, reducing latency and enabling faster decision-making.
IoT Integration: The proliferation of IoT devices and sensors will provide richer data for AI models, improving their predictive capabilities and enabling more comprehensive monitoring of equipment health.
Digital Twins: The concept of digital twins, which involves creating a virtual replica of physical assets, will facilitate more detailed and accurate simulations of equipment behavior, enhancing predictive maintenance efforts.
Collaborative AI: Collaborative AI systems that combine human expertise with machine intelligence will improve the effectiveness of predictive maintenance by leveraging the strengths of both humans and machines.
Competitive Analysis Table
Industry | Implementation of AI in Predictive Maintenance | Key Benefits | Challenges | Examples |
Manufacturing | Monitoring critical machinery | Reduced downtime, cost savings | Data quality, integration complexity | Global manufacturing companies |
Energy | Monitoring turbines, power plants | Increased availability, safety | Scalability, |
interoperability | Wind energy companies, power plants | | Aviation | Monitoring aircraft engines and systems | Improved reliability, reduced disruptions | Data volume, regulatory compliance | Major airlines and aircraft manufacturers | | Automotive | Monitoring vehicle components and systems | Enhanced safety, extended component life | Data diversity, technical expertise | Leading car manufacturers and fleet operators| | Oil and Gas | Monitoring drilling equipment and pipelines | Preventive failure, cost reduction | Harsh environments, data collection | Offshore drilling companies, pipeline operators |
Strategic Analysis Table
Strategy | Description | Benefits | Challenges |
Data Integration | Ensuring seamless integration of AI systems with existing infrastructure | Comprehensive data analysis, holistic insights | Complex integration processes, interoperability issues |
Edge Computing | Real-time data processing at the source of data collection | Low latency, quick decision-making | Hardware costs, limited processing power |
Advanced Algorithms | Utilizing sophisticated machine learning and deep learning models | High prediction accuracy, improved reliability | Requires specialized expertise, computationally intensive |
Human-Machine Collaboration | Combining human expertise with AI-driven insights | Enhanced decision-making, improved outcomes | Cultural resistance, training requirements |
IoT and Sensor Deployment | Increasing the number and variety of sensors for comprehensive monitoring | Rich data collection, detailed equipment health insights | Sensor maintenance, data management complexity |
AI’s integration into predictive maintenance is reshaping industries by transforming traditional maintenance practices into proactive, data-driven strategies. By addressing the challenges and leveraging the benefits, organizations can fully realize the potential of AI in predictive maintenance, ensuring operational efficiency, cost savings, and enhanced safety. The future of AI in predictive maintenance is bright, with continuous advancements and innovative applications paving the way for smarter and more reliable maintenance solutions.
Conclusion
AI is revolutionizing predictive maintenance by providing data-driven insights that enable proactive maintenance strategies. While the implementation of AI in vatic maintenance comes with challenges, the benefits far outweigh the obstacles. As AI technologies continue to advance, the future of predictive maintenance holds immense potential for improving operational efficiency, reducing costs, and enhancing safety across various industries. By embracing AI-driven predictive maintenance, organizations can achieve a competitive edge and ensure the reliability and longevity of their critical assets.