Introduction
3D printing, or additive manufacturing, has revolutionized the manufacturing industry, enabling rapid prototyping, reducing material waste, and facilitating the production of complex geometries that traditional manufacturing methods cannot achieve. This technology has evolved from a niche prototyping tool to a crucial component in the industry, offering immense benefits across various sectors, including automotive, aerospace, healthcare, and consumer goods. This article explores the transformative impact of 3D printing on manufacturing, emphasizing its benefits, real-world examples, and insightful case studies.
Understanding 3D Printing in Manufacturing
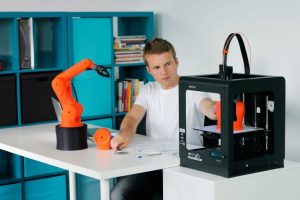
3D printing in manufacturing involves creating three-dimensional objects by layering materials based on digital models. Unlike traditional subtractive manufacturing, which removes material to create parts, 3D printing builds components from the ground up. This innovative approach allows for the design of intricate shapes and the integration of lightweight structures, all while reducing production costs and timelines.
Key Benefits of 3D Printing in Manufacturing
1. Rapid Prototyping and Product Development
One of the most significant advantages of 3D printing is its capability for rapid prototyping. Traditional prototyping can be time-consuming and costly, particularly when creating complex models. With 3D printing, companies can create prototypes quickly, test functionality, and make design adjustments with minimal delay.
- Example: The automotive industry uses 3D printing to rapidly develop prototype parts for new car models. Ford, for example, has leveraged 3D printing to create functional prototypes, reducing the time needed to design, test, and refine parts.
2. Cost-Effective Manufacturing
3D printing reduces costs by minimizing material waste and eliminating the need for specialized tooling. Traditional methods often require molds or custom tools for each component, but 3D printing only requires a digital design and raw material.
- Example: Boeing has incorporated 3D-printed components in its aircraft production to reduce costs associated with traditional manufacturing techniques. By using 3D-printed components, Boeing has managed to cut expenses on tooling, making the production process leaner and more cost-effective.
3. Customizability and Flexibility
3D printing offers unparalleled customization. Companies can easily adjust designs without reconfiguring complex machinery, enabling manufacturers to meet specific requirements for clients or produce limited-edition products.
- Case Study: In the healthcare industry, 3D printing has allowed for the production of personalized medical devices, such as prosthetics and implants. Companies like Align Technology use 3D printing to create customized Invisalign aligners for dental patients. This process tailors each product to the unique specifications of an individual’s dental structure, enhancing patient outcomes.
4. Reduced Material Waste and Environmental Impact
With sustainability becoming a priority, 3D printing offers an eco-friendly alternative to traditional manufacturing. This process uses only the material required to create an object, which reduces waste and conserves resources.
- Example: Adidas has partnered with Carbon, a 3D-printing technology company, to produce Futurecraft 4D shoes using 3D-printed midsoles. This method minimizes excess material, reduces waste, and promotes sustainable production practices, aligning with Adidas’s environmental goals.
5. Enhanced Supply Chain and Logistics Efficiency
3D printing enables manufacturers to produce parts on-demand, reducing inventory costs and streamlining supply chains. By printing components locally, companies can minimize shipping times and avoid supply chain disruptions.
- Case Study: During the COVID-19 pandemic, hospitals faced shortages of essential medical supplies. Companies used 3D printing to produce parts like ventilator valves and face shields on-demand. This approach not only reduced logistical issues but also enabled rapid response to critical healthcare needs.
3D Printing Applications in Key Manufacturing Sectors
1. Aerospace and Defense
The aerospace industry was an early adopter of 3D printing technology. 3D-printed parts offer a high strength-to-weight ratio, crucial for applications where reducing weight can lead to significant cost savings in fuel.
- Example: GE Aviation uses 3D printing to manufacture fuel nozzles for its LEAP engines. Traditional manufacturing methods required assembling 20 separate parts, but with 3D printing, the nozzle can be produced as a single, lightweight component. This innovation has led to improved engine efficiency and reduced overall aircraft weight.
2. Automotive
In the automotive sector, 3D printing allows manufacturers to create complex components quickly, reducing time-to-market for new car models and enabling on-demand parts production.
- Case Study: Volkswagen has utilized 3D printing for custom tools, fixtures, and vehicle parts. By implementing 3D printing in production processes, Volkswagen has achieved a 67% reduction in tooling costs, with parts produced up to 95% faster than with traditional methods. This efficiency has supported the company’s commitment to innovation and flexibility in production.
3. Healthcare
Healthcare applications of 3D printing are transformative, particularly in producing custom medical devices and creating surgical models for complex procedures.
- Example: Stryker, a medical technology company, uses 3D printing to create custom orthopedic implants. These 3D-printed implants are designed to conform to a patient’s unique anatomy, enhancing surgical outcomes and reducing recovery times.
4. Consumer Goods
The consumer goods industry leverages 3D printing to create customized products, limited editions, and prototypes for new designs.
- Case Study: Gillette, a leading razor manufacturer, introduced a pilot program called Razor Maker™, allowing customers to design and order custom 3D-printed razor handles. This program highlighted 3D printing’s potential for personalization, letting consumers create products tailored to their preferences.
Challenges Facing 3D Printing in Manufacturing
Despite its benefits, 3D printing in manufacturing faces several challenges:
- Material Limitations: Not all materials can be 3D-printed, limiting the application range. Metals, ceramics, and specific polymers have specific processing requirements that can complicate production.
- High Initial Costs: While 3D printing reduces long-term costs, initial setup and equipment investments can be significant, especially for small and medium-sized enterprises (SMEs).
- Quality and Consistency: Maintaining consistent quality in 3D-printed parts can be challenging, as minor variations in production settings or materials can affect output.
Future Prospects of 3D Printing in Manufacturing
3D printing continues to evolve, with innovations like multi-material printing, faster production speeds, and new material options. Emerging trends suggest that 3D printing will become even more accessible and adaptable to diverse manufacturing environments.
Key Trends Shaping the Future of 3D Printing in Manufacturing:
- Hybrid Manufacturing: Combining 3D printing with traditional manufacturing methods to leverage the strengths of both approaches.
- Mass Customization: As 3D printing becomes more cost-effective, mass customization could become a reality, allowing consumers to receive tailored products at scale.
- Sustainable Production: Future advancements in recyclable and biodegradable materials could make 3D printing an even more sustainable option for manufacturers.
Conclusion
3D printing is undeniably reshaping the manufacturing landscape. Its benefits — from cost reduction and rapid prototyping to customization and environmental sustainability — provide manufacturers with unprecedented opportunities to innovate. As illustrated by the cases of Boeing, Adidas, and Gillette, industries across the board are finding new ways to integrate 3D printing into their operations, pushing the boundaries of what’s possible. Despite facing challenges, ongoing advancements in materials, speed, and scalability promise to make 3D printing a cornerstone of modern manufacturing.
By embracing 3D printing, manufacturers can stay competitive in an evolving industry and offer products that are more innovative, sustainable, and responsive to market demands. The future of 3D printing in manufacturing is bright, with limitless potential to transform production processes and redefine the standards of efficiency and creativity.