Advancements in Digital Twin Technology for Manufacturing
In the fast-evolving world of manufacturing, technology continues to reshape how businesses operate, improve efficiency, and adapt to new challenges. One such transformative technology is digital twin technology. This powerful tool enables manufacturers to create virtual replicas of physical objects, systems, or entire production lines. These virtual models, known as digital twins, simulate the real-world processes in real time, providing valuable insights that improve decision-making, reduce downtime, and optimize production efficiency.
In this article, we will explore the latest advancements in digital twin technology for manufacturing, highlighting its benefits, real-world applications, and case studies demonstrating its impact on industries worldwide.
Introduction to Digital Twin Technology in Manufacturing
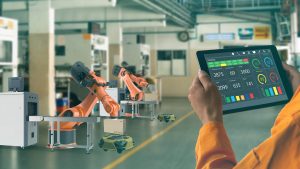
Digital twin technology is not new, but its capabilities and applications have evolved significantly in recent years. At its core, a digital twin is a virtual representation of a physical object or system that uses real-time data to simulate its behavior, condition, and performance. This digital model can be used for monitoring, predicting, and optimizing physical assets in various industries, including manufacturing, automotive, aerospace, and more.
In manufacturing, digital twins create a digital model of a machine, production line, or entire factory that reflects real-world operations in a simulated environment. This connection between the physical and digital worlds enables manufacturers to make informed decisions based on real-time data, rather than relying on assumptions or historical data alone.
Real-Time Data Integration: Revolutionizing Manufacturing Processes
One of the most significant advancements in digital twin technology is the integration of real-time data into virtual models. This integration allows manufacturers to monitor and manage their operations more efficiently.
Real-time data integration comes from the growing number of sensors, IoT devices, and connected machines within the production environment. These sensors continuously capture data such as machine temperature, vibration, speed, and wear and tear, transmitting it to the digital twin. This flow of information enables manufacturers to monitor the health of machines and the performance of production lines at all times.
Benefits:
- Predictive Maintenance: By analyzing real-time data, digital twins can predict when a machine is likely to fail or require maintenance. This prevents unplanned downtime, which can be costly for manufacturers.
- Optimized Performance: Real-time monitoring ensures that production lines run at peak efficiency, reducing the chances of bottlenecks or delays in manufacturing processes.
- Reduced Costs: Proactive maintenance and quick adjustments based on real-time data help reduce the costs of unexpected repairs and equipment replacements.
Example: Siemens and Digital Twins
Siemens, a global leader in automation, has implemented digital twin technology in their manufacturing plants to optimize production lines. By integrating real-time data from sensors into their digital twin models, Siemens is able to monitor the performance of machines and predict maintenance needs, resulting in a significant reduction in downtime and maintenance costs.
The Role of AI and Machine Learning in Digital Twin Technology
The integration of artificial intelligence (AI) and machine learning (ML) into digital twin technology has opened up new possibilities for predictive analytics and automation. AI and ML can analyze large volumes of data generated by the digital twin to identify patterns, predict outcomes, and suggest improvements.
AI algorithms can make sense of vast amounts of data in real-time, enabling manufacturers to detect potential issues that may not be visible to the human eye. These technologies help optimize production schedules, reduce waste, and improve overall system performance.
Benefits:
- Predictive Analytics: AI and ML models can predict failures or disruptions before they happen, allowing manufacturers to take preventive action.
- Process Optimization: These technologies help improve production efficiency by optimizing variables such as machine speed, material flow, and workforce allocation.
- Continuous Improvement: As more data is collected, machine learning algorithms continuously improve the accuracy of the digital twin, leading to better predictions and optimizations over time.
Case Study: General Electric (GE)
General Electric uses AI-powered digital twins for predictive maintenance in the aerospace sector. By leveraging machine learning algorithms, GE monitors real-time data from engines and components, predicting when maintenance is needed and optimizing the maintenance schedules. This approach has helped GE reduce maintenance costs and improve engine performance across its fleet of aircraft.
Edge Computing: Enhancing Speed and Efficiency in Digital Twin Systems
Edge computing is another technological advancement that complements digital twin technology. Edge computing involves processing data closer to its source, rather than sending it to a centralized cloud server. This allows for faster data analysis and decision-making.
In manufacturing, edge computing enables real-time data processing at the machine or production line level, ensuring that decisions can be made quickly, even in environments with low connectivity or high data volumes. By reducing latency, manufacturers can make timely adjustments and optimize their processes without delays.
Benefits:
- Faster Decision-Making: With edge computing, manufacturers can make adjustments to the production process almost instantly, ensuring that systems remain efficient and responsive.
- Improved Reliability: Edge computing helps prevent data bottlenecks by processing information locally, which improves system reliability and reduces downtime.
- Reduced Bandwidth Costs: By processing data at the edge, only critical information needs to be sent to centralized systems, reducing bandwidth usage and cloud storage costs.
Example: Bosch and Edge Computing
Bosch uses edge computing in their smart factories to process data from manufacturing machines locally. This has allowed them to make real-time adjustments to production processes, improving efficiency and reducing energy consumption. Bosch’s approach highlights how edge computing and digital twins work together to optimize factory operations.
Advanced Simulation and Testing Capabilities
The ability to simulate various scenarios before implementing them in the real world is another advantage of digital twin technology. Advanced simulation capabilities allow manufacturers to test changes in production lines, materials, or processes virtually, without incurring the cost or risk associated with physical trials.
Simulation enables manufacturers to identify potential bottlenecks, optimize workflows, and determine the best strategies for production and supply chain management. It also helps in designing and testing new products before they are physically created, ensuring better design quality and performance.
Benefits:
- Risk Reduction: Simulating different production scenarios helps manufacturers identify risks and address them before real-world implementation.
- Cost Efficiency: Virtual testing eliminates the need for costly physical prototypes and trials, speeding up the development process and reducing costs.
- Faster Time to Market: By using digital twins for product testing and simulations, manufacturers can bring products to market faster while ensuring quality and efficiency.
Case Study: Ford Motor Company
Ford uses digital twins to simulate the entire vehicle manufacturing process. By modeling different production scenarios and testing vehicle designs virtually, Ford has improved its ability to produce high-quality cars more efficiently, reducing the time required to bring new models to market.
Improving Sustainability and Energy Efficiency Through Digital Twins
Sustainability has become a critical concern for manufacturers worldwide. Digital twin technology plays a pivotal role in helping manufacturers achieve their sustainability goals. By simulating energy usage, waste management, and production processes, digital twins help companies optimize operations to minimize environmental impact.
Digital twins also allow manufacturers to monitor and manage their carbon footprint, track resource usage, and design more energy-efficient systems and products. This not only helps companies align with sustainability goals but also ensures compliance with increasingly stringent environmental regulations.
Benefits:
- Energy Optimization: Digital twins can simulate energy usage, helping manufacturers optimize production processes for energy efficiency and lower costs.
- Waste Reduction: By analyzing production data, digital twins can identify areas where material waste can be minimized.
- Sustainability Reporting: Manufacturers can use digital twins to track sustainability metrics and ensure compliance with environmental standards.
Example: Philips Lighting
Philips Lighting uses digital twins to optimize the energy usage of its smart lighting solutions. By simulating the performance of lighting systems in different environments, they can fine-tune their designs to be more energy-efficient, helping their customers reduce energy consumption and lower carbon footprints.
Digital Twins for Remote Monitoring and Global Collaboration
Digital twin technology also enhances collaboration and remote monitoring in manufacturing. With cloud-based digital twins, teams across the globe can access the same virtual models, making it easier to troubleshoot, optimize, and collaborate on production processes.
Engineers and operators no longer need to be physically present at the site to monitor machine performance or resolve issues. Remote monitoring ensures that issues can be identified and addressed from anywhere, significantly improving operational efficiency and reducing downtime.
Benefits:
- Improved Collaboration: Cloud-based digital twins enable real-time collaboration across teams in different locations.
- Remote Troubleshooting: Engineers can remotely diagnose and resolve production issues without having to be physically present, reducing response time.
- Increased Productivity: Remote monitoring and collaboration enable a more flexible and agile workforce, enhancing overall productivity.
Supply Chain Management and Digital Twin Integration
Digital twins also extend beyond the factory floor, playing a critical role in supply chain management. By integrating data from suppliers, logistics, and production lines, digital twins provide a comprehensive view of the supply chain in real-time, improving decision-making and visibility.
With a digital twin of the entire supply chain, manufacturers can simulate different scenarios, identify potential disruptions, and optimize logistics to reduce delays and costs. This level of visibility helps improve the resilience of supply chains, especially in times of uncertainty.
Benefits:
- Supply Chain Optimization: Digital twins allow for better decision-making in logistics, from raw material sourcing to delivery.
- Risk Management: Simulating supply chain disruptions helps manufacturers plan and mitigate risks in advance.
- Improved Efficiency: Digital twins help reduce delays and streamline the movement of goods across the supply chain.
Example: Nike
Nike uses digital twins to optimize its global supply chain. By creating virtual models of its suppliers and distribution networks, Nike is able to quickly adjust to changes in demand or supply chain disruptions, ensuring that products reach customers on time.
Blockchain in Digital Twin Technology for Enhanced Security
As digital twin technology relies heavily on data, ensuring its security is crucial. Blockchain technology is increasingly being integrated into digital twin systems to enhance data integrity and security. Blockchain provides a decentralized, transparent, and immutable record of all transactions and data exchanges, making it ideal for protecting sensitive manufacturing data.
By using blockchain, manufacturers can ensure that the data collected from sensors and machines is accurate, tamper-proof, and securely shared between parties.
Benefits:
- Data Integrity: Blockchain ensures the accuracy and security of data, preventing tampering or unauthorized access.
- Transparency: Blockchain provides a transparent record of data exchanges, ensuring traceability and accountability.
- Secure Data Sharing: Blockchain enables secure sharing of data between different stakeholders without compromising privacy or security.
The Future of Digital Twin Technology in Manufacturing
As digital twin technology continues to evolve, its applications and capabilities are expanding. The future of digital twins in manufacturing will likely include even more advanced simulation tools, greater integration with AI and ML, and increased use of blockchain for data security.
Manufacturers are also likely to see wider adoption of customizable and scalable digital twin solutions, making the technology accessible to businesses of all sizes. As more industries adopt digital twins, we can expect to see innovative new applications that further enhance the efficiency, sustainability, and safety of manufacturing operations.
Conclusion
Digital twin technology is revolutionizing the manufacturing industry by enabling real-time monitoring, predictive maintenance, process optimization, and much more. The integration of AI, machine learning, edge computing, and blockchain is making digital twins more accurate, secure, and effective. As manufacturers continue to adopt and advance digital twin technology, the future looks bright for more efficient, sustainable, and innovative manufacturing practices.
By leveraging these advancements, manufacturers can stay ahead of the curve, improve operations, and create new opportunities in the increasingly digital and interconnected world of manufacturing.
FAQs
What is a digital twin in manufacturing?
A digital twin in manufacturing is a virtual model of a physical object or system that mirrors real-time data from the real-world counterpart, allowing for simulation, optimization, and monitoring.
How does real-time data integration improve manufacturing?
Real-time data integration allows manufacturers to monitor machine health, predict failures, and optimize performance, leading to reduced downtime and improved efficiency.
What role do AI and machine learning play in digital twins?
AI and machine learning analyze large data sets from digital twins, predicting outcomes and optimizing processes, which helps manufacturers improve decision-making and efficiency.
What is edge computing, and how does it help digital twins?
Edge computing processes data closer to its source, reducing latency and enabling faster decision-making for real-time adjustments and improved production efficiency.
How can digital twins improve sustainability in manufacturing?
Digital twins help optimize energy usage, reduce waste, and track sustainability metrics, contributing to more environmentally-friendly and cost-effective manufacturing practices.