The integration of Digital Twin Technology in smart factories is revolutionizing the manufacturing landscape. One of the most significant advantages is enhanced predictive maintenance. Digital Twin Technology allows for the creation of a virtual replica of physical assets, which can be used to monitor and predict equipment performance. By analyzing real-time data, manufacturers can anticipate potential failures before they occur, thus scheduling maintenance proactively. This not only extends the lifespan of equipment but also reduces unexpected breakdowns, thereby ensuring a smoother production process.
Optimized production processes are another noteworthy benefit of Digital Twin Technology in smart factories. By simulating different production scenarios, manufacturers can identify bottlenecks and inefficiencies in the production line. This enables them to make data-driven decisions to optimize the entire manufacturing process. Through these simulations, manufacturers can explore various configurations and select the most efficient one, leading to increased productivity and reduced operational costs.
Enhancing Predictive Maintenance with Digital Twins
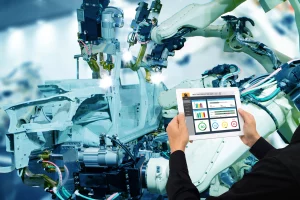
Optimizing equipment lifespan with Digital Twin Technology is a game-changer in the realm of predictive maintenance. By continuously monitoring the condition of machinery and equipment, Digital Twins provide valuable insights into wear and tear patterns. This information allows manufacturers to schedule maintenance activities at the most opportune times, thus avoiding premature replacement of parts and extending the overall lifespan of the equipment. The ability to predict when a machine is likely to fail ensures that maintenance is performed only when necessary, leading to significant cost savings.
Reducing downtime through predictive maintenance with Digital Twins is another critical advantage. Unplanned downtime can be extremely costly for manufacturers, leading to production delays and financial losses. Digital Twin Technology helps mitigate this risk by providing real-time data on the health of machinery. By identifying potential issues before they escalate into major problems, manufacturers can perform maintenance during scheduled downtimes, thus minimizing disruptions to the production process. This proactive approach ensures that machinery operates at peak efficiency, reducing overall downtime and improving productivity.
Real-time Data Analytics for Manufacturing
Enhancing real-time analytics with Digital Twin Technology is transforming how manufacturers approach data-driven decision-making. Digital Twins collect and analyze vast amounts of data from various sensors and devices in real-time. This continuous stream of data provides manufacturers with a comprehensive view of their operations, enabling them to identify trends, anomalies, and areas for improvement. With real-time analytics, manufacturers can make informed decisions quickly, optimizing their processes and responding to changes in the production environment more effectively.
Optimizing manufacturing processes using Digital Twin Technology is a direct result of enhanced real-time analytics. By leveraging the insights gained from Digital Twins, manufacturers can fine-tune their production processes to achieve maximum efficiency. For example, they can adjust machine settings, streamline workflows, and allocate resources more effectively based on real-time data. This level of optimization not only improves productivity but also reduces waste and operational costs, leading to a more sustainable and profitable manufacturing operation.
Optimizing Production Processes through Simulation
Digital Twin Technology enhances production process optimization through simulation, providing manufacturers with a powerful tool to test and refine their processes. By creating a virtual model of the production line, manufacturers can simulate various scenarios and evaluate their impact on efficiency and output. This allows them to identify potential bottlenecks, test different configurations, and implement changes without disrupting actual production. The ability to simulate and optimize processes in a virtual environment leads to significant improvements in overall efficiency and productivity.
Simulation with Digital Twin Technology predicts future manufacturing scenarios, enabling manufacturers to stay ahead of potential challenges. By analyzing historical data and simulating future conditions, Digital Twins can forecast potential issues and provide insights into how different factors may impact production. This predictive capability allows manufacturers to develop contingency plans and make proactive adjustments to their processes, ensuring that they are well-prepared for any future disruptions. The ability to anticipate and respond to changes in the manufacturing environment is a key advantage of Digital Twin Technology.
Reducing Downtime and Increasing Efficiency
Digital Twin Technology minimizes machine downtime via predictive maintenance by providing real-time insights into the health and performance of machinery. By continuously monitoring equipment and analyzing data, Digital Twins can detect early signs of wear and potential failures. This allows manufacturers to schedule maintenance activities proactively, reducing the likelihood of unexpected breakdowns and minimizing downtime. The ability to predict and prevent issues before they occur ensures that machinery operates at peak efficiency, leading to improved productivity and reduced operational costs.
Digital Twin Technology enhances operational efficiency with real-time data insights, enabling manufacturers to make informed decisions quickly. By collecting and analyzing data from various sources, Digital Twins provide a comprehensive view of the manufacturing process. This real-time visibility allows manufacturers to identify inefficiencies, optimize workflows, and allocate resources more effectively. The ability to make data-driven decisions in real-time ensures that production processes continuously optimized, leading to increased efficiency and reduced waste.
Customization and Flexibility in Manufacturing
Digital Twin Technology enables real-time customization in manufacturing, allowing manufacturers to meet the growing demand for personalized products. By creating virtual models of products and production processes, manufacturers can quickly adapt to changes in customer requirements and preferences. This flexibility enables them to produce customized products on-demand, reducing lead times and improving customer satisfaction. The ability to offer real-time customization is a significant competitive advantage in today’s dynamic market.
Flexibility is enhanced through Digital Twin Technology in production processes, allowing manufacturers to respond quickly to changes in demand and production conditions. By simulating different scenarios and evaluating their impact on the production line, manufacturers can make informed decisions about how to allocate resources and adjust processes. This flexibility ensures that manufacturers can adapt to changing market conditions and maintain efficient production, even in the face of unexpected challenges. The ability to quickly and effectively respond to changes is a key benefit of Digital Twin Technology.
Sustainability and Resource Management
Sustainability through Digital Twin Technology in resource management is becoming increasingly important for manufacturers. By providing real-time insights into resource usage, Digital Twins enable manufacturers to optimize their consumption of energy, water, and raw materials. This not only reduces operational costs but also minimizes the environmental impact of manufacturing processes. The ability to monitor and manage resources more effectively is a critical component of sustainable manufacturing practices.
Optimizing resource usage with Digital Twin Technology in manufacturing is a key advantage for manufacturers looking to improve efficiency and reduce waste. By analyzing data on resource consumption and production processes, Digital Twins can identify areas where resources being used inefficiently. Manufacturers can then implement changes to optimize resource usage, reducing waste and lowering operational costs. The ability to use resources more effectively is a significant benefit of Digital Twin Technology, contributing to both sustainability and profitability.
Future Trends in Digital Twin Technology
The integration of AI in Digital Twin Technology for manufacturing is poised to take predictive maintenance and process optimization to the next level. By combining the power of AI with Digital Twins, manufacturers can analyze vast amounts of data more quickly and accurately. AI algorithms can identify patterns and trends that may not be apparent to human analysts, providing deeper insights into equipment performance and production processes. The integration of AI enhances the predictive capabilities of Digital Twins, enabling manufacturers to make more informed decisions and optimize their operations more effectively.
Enhanced predictive maintenance using Digital Twin Technology is a key trend that is shaping the future of manufacturing. As Digital Twins become more sophisticated, their ability to predict equipment failures and maintenance needs will continue to improve. This will enable manufacturers to move from reactive to proactive maintenance strategies, reducing downtime and extending the lifespan of machinery. The ongoing advancements in Digital Twin Technology will continue to drive improvements in predictive maintenance, leading to more efficient and reliable manufacturing processes.