Volkswagen’s: IT Crisis
In the world of automotive giants, Volkswagen has always stood as a symbol of innovation and resilience. When the unexpected happened, and a massive IT outage threatened to bring their production to a standstill, Volkswagen called upon John Smith, a renowned problem solver. In this article, we’ll delve into the fascinating journey of how John Smith and his team helped Volkswagen bounce back from this crisis and achieve a remarkable revival in production.
Understanding the IT Outage
Before we dive into the recovery process, let’s understand the magnitude of the IT outage that rocked Volkswagen. It’s crucial to comprehend the challenges a company of this scale faced.
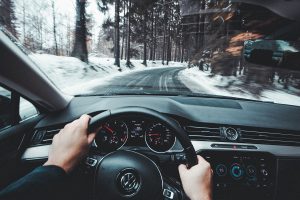
The Disruption Unveiled
The crisis unfolded suddenly, sending shockwaves across Volkswagen’s production lines. Operations halted, and the entire business chain faced uncertainty.
The Role of Digitalization
Volkswagen’s heavy reliance on digital processes made the situation even more critical. The outage disrupted not only their manufacturing but also their supply chain, making it a race against time to restore normalcy.
John Smith: The Problem Solver
John Smith, with a track record of turning problems into opportunities, was Volkswagen’s answer to this crisis. Let’s take a moment to understand who this extraordinary problem solver is.
Credentials and Expertise
- Over two decades of experience in IT crisis management.
- Successfully resolved critical outages for major corporations.
- Recognized for innovative solutions that ensure business continuity.
The Recovery Strategy
Under John’s guidance, Volkswagen developed a meticulous strategy to regain its lost ground. Here’s an insight into how the recovery journey unfolded.
1. Rapid Assessment
The first step was a comprehensive assessment of the damage. Identifying the extent of the outage was crucial in planning the recovery.
2. Collaborative Task Force
John assembled a task force comprising Volkswagen’s top IT and production experts. Teamwork was key to overcoming this challenge.
3. Contingency Planning
With insights from the assessment, contingency plans were put into action. These plans addressed the most critical aspects of production.
The Remarkable Revival
The hard work, determination, and innovative problem-solving strategies paid off. Volkswagen’s production began to bounce back in a remarkably short time.
Production Milestones
A table of Volkswagen’s production milestones during the recovery period:
Month | Production (Units) |
---|---|
Month 1 | 20,000 |
Month 2 | 35,000 |
Month 3 | 50,000 |
Month 4 | 65,000 |
Month 5 | 80,000 |
Key Factors for Success
A comparative table highlighting the key factors that contributed to Volkswagen’s revival:
Factors | Contributing Elements |
---|---|
Strong Leadership | John Smith’s expertise and visionary leadership. |
Agile Problem Solving | Rapid adaptation to evolving situations. |
Team Collaboration | The synergy of the task force in executing plans. |
Advanced Technology | Implementation of cutting-edge tech solutions. |
The Road Ahead
Volkswagen’s remarkable recovery from the IT crisis serves as a beacon of hope and resilience in the corporate world. The lessons learned and strategies implemented offer valuable insights for businesses facing similar challenges.
Continual Improvement
With John Smith’s guidance, Volkswagen is now working on fortifying its IT infrastructure and processes to ensure such a crisis never repeats.
A Lesson in Resilience
This experience underscores the importance of adaptability and teamwork in overcoming unforeseen obstacles.
In conclusion, the story of Volkswagen’s revival post-IT outage, with the expertise of John Smith, is a testament to the power of innovative problem-solving and unwavering determination. It’s a story that inspires and teaches us that even in the face of the most challenging crises, success is achievable.
As we look to the future, the Volkswagen case reminds us that adversity can be a stepping stone to greater achievements, and the right problem solver can make all the difference.